Sandwich panels
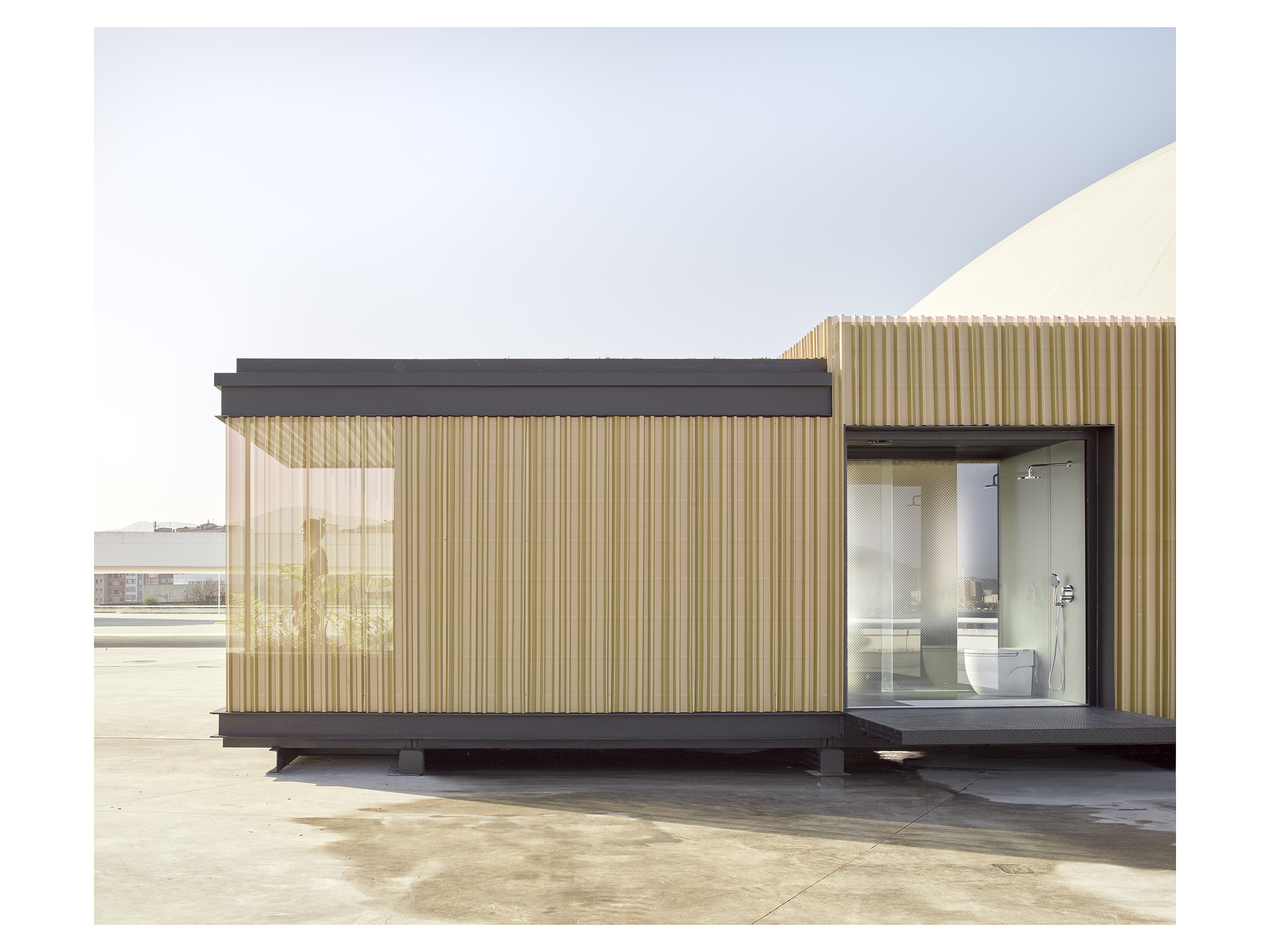
Sandwich panels are assembled roof and wall elements that have excellent insulating characteristics thanks to the integration of insulating material. They consist of two thin metal cover sheets, which are shear-resistant and are bonded to one another on an insulated core. The insulated cores normally consist of hard polyurethane foam (PUR), hard polystyrene foam and mineral wool (MW) as well in order to meet the fire prevention requirements. Sandwich panels are produced by continuously running production plants and sawn to ordered lengths. The surfaces can also contain lined, trapezoidal or corrugated profiles, depending on the customer’s requirements. They are manufactured as both roof and wall elements. Sandwich panels can be produced with visible fastenings and with non-visible fastenings as well. The non-visible fastenings enable architecturally appealing facades to be created without the visual appearance being ruined by rows of screws. The excellent insulating characteristics combined with the array of systems, the quality and the appealing visual appearance have resulted in continuous spread of the use of these structural elements.
U-values ranging up to 0.12 W/(m²K) can be realised, depending on the thickness of the panel. The space between the supports can be up to 11 m (walls), depending on the type of panel used. Normal applications have spaces between the supports that are approx. 3 m – 5 m. The assessed sound reduction measurement lies at approx. 25 dB for PUR elements and at approx. 30 dB for MW elements. Steel sandwich panels with polyurethane have shown in various fire tests that they do not contribute to the cause of fires. Mineral wool sandwich panels are available up to fire resistance class EI 120 in order to meet the various fire prevention requirements.